Important Considerations for Replacing Parts in Diesel Generator Sets
On this page
Diesel generator sets play an essential role as vital power equipment across various sectors. Whether in industrial production, commercial operations, or emergency power systems, the stability and reliability of these generators directly impact operational efficiency and safety. However, over time, components of the generator sets inevitably experience wear and tear or malfunction, making timely maintenance and part replacement crucial.
This article will explore the key considerations to focus on during the replacement of parts in diesel generator sets, ensuring the normal operation of the equipment and extending its lifespan. By adhering to these professional guidelines, maintenance personnel can effectively prevent potential issues and enhance the overall performance of the generator sets.
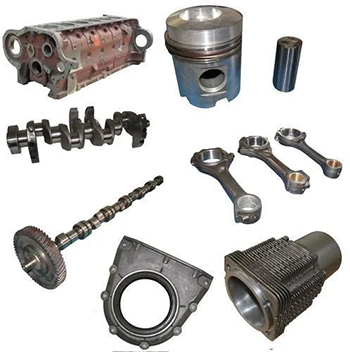
Cleaning is vital before replacing any parts in a diesel generator set. Contaminants such as dust, oil, or metal debris can cause significant wear on components and may lead to issues like clogged oil lines or damaged bearings. Here are some cleaning steps to follow.
Cleaning Parts: Use a dedicated cleaning agent to thoroughly clean the parts being replaced, ensuring they are free of oil and debris. Consider using brushes or ultrasonic cleaners to reach difficult areas.
Organizing the Work Environment: Keep the workbench and tools clean to prevent dirt from entering the engine. Regularly tidy the work area to minimize potential contamination.
Using Dust Prevention Measures: During disassembly and reassembly, cover important components with dust covers or cloths to reduce dust exposure. Additionally, consider employing anti-static measures to protect electronic parts.
When replacing parts, it is crucial to verify that the new components are compatible with the generator set. Different models may have non-interchangeable parts, and choosing the wrong ones can lead to performance issues or severe failures.
Model Matching: Ensure that the purchased parts exactly match the generator set model, especially critical components like crankshafts, main bearings, and pistons. Check part numbers and technical specifications for accuracy.
Choosing Original Parts: Opt for original manufacturer parts or certified replacements to ensure quality and compatibility. While non-original parts might seem cost-effective in the short term, they can lead to higher failure rates and maintenance costs in the long run.
Ensuring that replacement parts are the correct size is essential. Incorrect sizing can affect assembly quality and the lifespan of the components.
Following Technical Specifications: Refer to the manufacturer's technical manual to confirm that part sizes meet requirements. Understand the tolerance ranges for different components to ensure selected parts fall within acceptable limits.
Using Measurement Tools: Employ precise measurement tools like calipers and gauges to verify part sizes. If necessary, take multiple measurements to ensure consistency and accuracy.
Following specific assembly technical requirements is key to ensuring the proper operation of the generator set.
Installing Cylinder Liners: When installing cylinder liners, ensure the top surface is approximately 0.1mm above the engine block to prevent leaks or gasket damage. Use a thickness gauge to assist in achieving accuracy.
Gap Control: Strictly monitor parameters like valve and bearing clearances to ensure they are within normal ranges, avoiding failures caused by improper gaps. Use specialized tools to measure and adjust these gaps accurately.
When replacing components like injector nozzles, plungers, and oil outlet valves, it's crucial to follow the principle of paired replacement. This ensures compatibility and prevents issues arising from replacing only one side.
Replacing Gears: When changing gears, always replace a worn gear pair together to ensure proper engagement and avoid noise or excessive wear. Assess wear levels to determine if the entire gear set needs replacement.
Sealing Component Replacement: If sealing components are present, it's advisable to replace them simultaneously to maintain system integrity and prevent leaks. This is especially critical in high-pressure or high-temperature applications.
A diesel generator set consists of thousands of parts, each with specific installation positions and orientation requirements. Misinstallation or omission can lead to starting difficulties or failure to start altogether. Therefore, it's important to:
Clarify Component Positioning: Familiarize yourself with each part's function and its position in the system before assembly. Marking positions can be helpful. Use checklists or diagrams to assist maintenance personnel in confirming each part's installation location.
Conducting Thorough Checks: After installation, systematically check each part's installation to ensure everything is correctly positioned. Conducting a test run can help identify potential issues.
Replacing parts in a diesel generator set is a complex task requiring high levels of expertise. By keeping parts clean, checking compatibility, selecting the right sizes, adhering to technical requirements, replacing paired components, avoiding misinstallation, and conducting regular maintenance, you can effectively ensure the generator set operates smoothly and reliably. Thorough and detailed maintenance not only extends the lifespan of the generator set but also provides dependable power support across various applications. By rigorously following these guidelines, maintenance personnel can better manage the performance of diesel generator sets, ensuring efficient operation in diverse environments.