Diesel Generator Starter Motors: Faults and Maintenance
On this page
The starter motor of a diesel generator plays a critical role in the startup process. It converts the electrical energy from the battery into mechanical energy to provide initial power for the generator, driving the flywheel and enabling the diesel generator engine to start. However, after prolonged use, the starter motor may experience various issues that can reduce its performance or even prevent it from starting. This article will explore the working principles of the starter motor, common faults, diagnostic and troubleshooting methods, and repair steps.
Diesel generators require external force to initiate startup, and the starter motor fulfills this essential function. Its main role is to use battery power to rotate the generator's flywheel, supplying the necessary mechanical energy for startup. The starter motor comprises three core components.
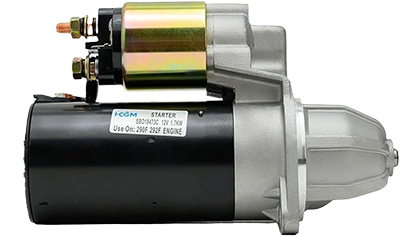
The motor draws current from the battery and converts it into mechanical motion, rotating the drive gear in the starter motor.
This mechanism engages the drive gear with the flywheel ring gear to initiate the engine. Once the engine starts, it automatically disengages to prevent unnecessary wear on both the starter motor and flywheel.
The electromagnetic switch controls the starter motor circuit, regulating the power flow during startup and ensuring stable current while preventing overload.
During generator startup, the starter motor may encounter various issues, including:
Symptoms include the drive gear not turning or turning slowly. Possible causes:
Electrical line faults preventing current flow.
Burnt starter switch contacts hindering current conduction.
Excessive engine resistance preventing the starter motor from engaging the flywheel.
When the starter motor lacks output power, the crankshaft cannot turn smoothly. Common causes include:
Shorted or damaged excitation coil, reducing the magnetic field strength.
Insufficient or aging battery, unable to provide adequate current.
If the starter motor produces abnormal noise, possible causes are:
Jammed one-way clutch causing operational issues.
Improper installation leading to poor transmission.
This could result from low battery charge, poor cable connections, or inadequate battery cable quality. Other possible causes include excess oil in the oil pan, severely worn brushes, or poor contact in the magnetic switch.
When a diesel generator fails to start, the following methods can help diagnose the starter motor's faults.
Use a voltmeter to check the voltage at each point in the starter circuit. If the voltage drop exceeds 0.2V during startup, it may indicate excessive contact resistance. Clean all terminals and apply lubricant on battery posts and cable clamps to slow down corrosion.
Measure the starter motor's no-load speed with a tachometer and compare it to the manufacturer's specifications. Low speed may indicate bearing damage or high contact resistance in the circuit.
Inspect the starter button and ignition key for contact issues. Check for any broken wires or blown fuses in the starter circuit.
Examine brush wear and spring pressure, ensuring they meet specifications. Use a short-circuit tester to check for shorts in the armature coil and inspect the commutator for burns.
To maintain efficient starter motor operation, disassembly and repair may be necessary. Basic steps include:
Disconnect the battery to avoid short circuits during disassembly. Use appropriate tools to detach the starter motor from the engine, marking wires to ensure correct reconnection if the electromagnetic switch is attached.
Remove the front and rear covers to access internal components. Check the excitation coil for shorts, breaks, or grounding issues, and use an ohmmeter to measure its resistance, comparing it to the manufacturer's specs.
Brushes: Check for wear and replace if necessary, ensuring spring pressure meets requirements.
One-Way Clutch: Ensure it rotates smoothly in the free direction and locks instantly in the locking direction, with free axial movement.
Bushings: Replace worn bushings to avoid increased current and abnormal noise during startup.
If the commutator shows signs of burning, polish with fine sandpaper or use a lathe to smooth it. After removing burrs, reassemble the starter motor.
Clean all parts before assembly, applying high-temperature grease to the bushings. Assemble components following the manufacturer's recommended sequence to ensure secure connections.
Start the diesel generator and check if the starter motor operates smoothly. If it works well, the repair is complete. Otherwise, further inspection of the circuit and mechanical parts is needed.
To extend the starter motor's lifespan and ensure reliable generator startups, regular maintenance is recommended.
Periodically check the battery charge and cable connections, clean electrodes, and apply lubricant.
Regularly inspect brush and commutator wear, replacing as necessary.
Ensure secure installation to prevent vibration-related contact loosening.
Use standard-compliant battery cables to avoid current issues from undersized wires.
The starter motor is a vital component of the diesel generator's startup system. Proper diagnosis, repair, and routine maintenance can enhance its efficiency, prolonging its lifespan and providing reliable startup support for the generator. Timely troubleshooting not only improves generator performance but also reduces repair costs, ensuring that the generator is ready to perform when needed most.