Crankcase Blow-by in Diesel Generators and Its Management
On this page
Crankcase blow-by refers to the abnormal increase in gas flow within the crankcase during the operation of a diesel generator. It is commonly used to assess the technical condition and wear level of the cylinder piston assembly. The blow-by volume in the crankcase of a new engine is typically between 15 to 20 L/min, but in cases of severe wear, this value can reach 80 to 130 L/min. Controlling and managing crankcase blow-by is crucial for ensuring the normal operation of diesel generators, as it directly affects the engine's power and fuel consumption.
Understanding the causes and manifestations of crankcase blow-by is essential for effective maintenance and repair. Crankcase blow-by is the phenomenon where internal engine gases escape through the crankcase during operation. Here are the main causes of crankcase blow-by.
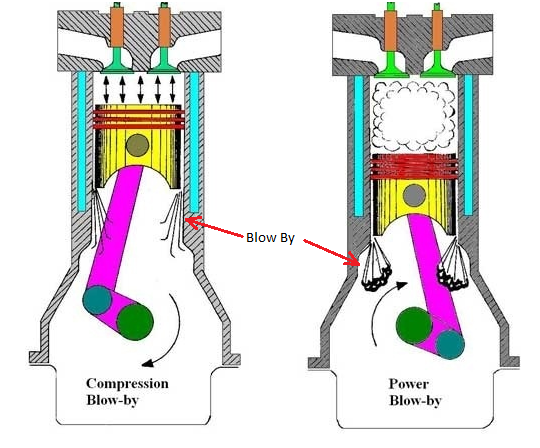
Valve and Valve Seat Clearance Leakage: As the clearance between the valve and valve seat increases due to wear or cracks appear in the cylinder head due to casting defects, gases may enter the valve chamber through these gaps or cracks, causing blow-by.
Valve Chamber Blow-by: Gases flow into the valve chamber from cracks or gaps in the cylinder block or head, forming blow-by.
Piston Ring Breakage or Seizure: If the piston ring breaks, seizes, or is improperly installed, the sealing effect rapidly decreases, and gases may flow into the crankcase from the gap of the broken ring or the gap between the ring and the cylinder liner.
Sudden Temperature Increase: Lack of water or water interruption can cause a sharp increase in cylinder temperature, potentially causing the piston, piston rings, and cylinder liner to stick together, leading to large-area scoring of the piston and causing blow-by.
Gasket Aging: The gasket may age or the cylinder block and head may corrode, leading to inadequate sealing between the head and the block, allowing compressed gases to enter the cooling waterways and oil passages through tiny gaps.
Microscopic Defects: Pits, scratches on the top surface of the cylinder block or the bottom surface of the cylinder head, uneven thickness of the gasket, or damage to the copper sheet can lead to inadequate sealing.
Oil Passage Burn Damage: Burn damage to the oil passage port of the gasket allows high-pressure gases to escape through the oil passage, entering the valve chamber at the top and the crankcase at the bottom, affecting lubrication efficiency.
The manifestations of crankcase blow-by can be identified in several ways, indicating not only the presence of blow-by but also reflecting the technical condition and potential issues of the engine. Here are common manifestations of crankcase blow-by.
Manifestation: Blow-by can be observed through the crankcase oil filler opening. Leakage between the valve and valve seat may cause gases to flow into the valve chamber. Severe blow-by is usually accompanied by a decrease in engine power and an increase in fuel consumption.
Inspection Method: Check the clearance between the valve and valve seat for wear or cracks, and inspect the cylinder head for defects.
Manifestation: Breakage or seizure of the piston ring can cause gases to flow into the crankcase from the gap of the broken ring or the gap between the ring and the cylinder liner, usually accompanied by a small amount of engine oil. Severe blow-by may result in a sudden increase in engine temperature.
Inspection Method: Dismantle and inspect the condition of the piston rings and cylinder liners to confirm if there are any breakages, seizures, or improper installations. Address and cool promptly to prevent further damage.
Manifestation: Blow-by between the cylinder head and block may cause compressed gases to enter the cooling waterways and oil passages, affecting the normal operation of the engine. This usually leads to a decrease in engine power and abnormalities in the cooling system.
Inspection Method: Inspect the cleanliness of the gasket and its mating surfaces, ensuring that the bolts are tightened evenly with the specified torque to avoid blow-by due to inadequate sealing.
Manifestation: High-pressure gases enter the valve chamber and crankcase through the damaged oil passage port. This phenomenon can lead to a deterioration in the lubrication efficiency of the crankshaft, camshaft, and rocker arm shaft, potentially causing serious faults such as seizure or bearing damage.
Inspection Method: Inspect the condition of the gasket and replace the damaged one promptly to eliminate oil passage blow-by, and ensure the lubrication system is functioning properly.
Addressing crankcase blow-by issues requires taking appropriate measures based on different causes to restore normal engine operation and prevent further damage. Here are the remedial measures for the main causes.
Inspection and Replacement: Regularly inspect and replace related components such as valves, valve seats, and valve guides. If wear or damage is found, timely replacement is necessary.
Cylinder Head Leak Repair: Repair cracks or gaps in the cylinder head to ensure that gases do not flow into the valve chamber through these defects.
Cooling and Inspection: In case of piston ring issues, immediately shut down the diesel generator and let it cool naturally to avoid continued operation. Dismantle and inspect the condition of the piston rings for replacement or adjustment.
Preventive Measures: Ensure that the piston rings are selected and installed properly to avoid poor sealing due to improper installation or selection.
Cleaning and Tightening: Inspect the mating surfaces of the gasket with the cylinder block and head, ensuring cleanliness and proper treatment. When tightening the cylinder head bolts, do so uniformly with the specified torque and perform a second tightening to ensure sealing effectiveness.
Gasket Replacement: Replace aged or damaged gaskets promptly to avoid blow-by caused by inadequate sealing.
Gasket Replacement: Replace damaged gaskets promptly to eliminate oil passage blow-by.
Lubrication Inspection: Ensure normal lubrication efficiency for the crankshaft, camshaft, and rocker arm shaft. Regularly check the quality and quantity of the lubricating oil to prevent mechanical damage due to insufficient lubrication.
Crankcase blow-by is a potential issue that diesel generators may encounter during use, directly affecting engine performance and lifespan. By regularly inspecting and maintaining valve components, piston rings, cylinder head and block sealing, and addressing vertical blow-by issues, blow-by phenomena can be effectively controlled and reduced, ensuring the normal operation and long-term use of diesel generators. When blow-by issues are detected, appropriate remedial measures should be taken according to the specific situation to ensure the healthy operation of the engine.