Assembly Process of Key Components in Diesel Generators
On this page
The performance and reliability of a diesel generator largely depend on the precise assembly of its core components. Operating under high-load conditions, the generator requires that critical parts, such as the piston and connecting rod assembly, oil pump, gear system, fuel injector, and torsional vibration damper, function together optimally. Each component must meet strict quality standards and be precisely installed in terms of alignment, clearance, and torque to ensure efficient and stable operation. By following standardized assembly processes and regular maintenance, diesel generators can achieve improved durability and performance, ensuring continuous, reliable power supply.
The piston and connecting rod assembly is critical to the generator's smooth operation and affects combustion efficiency and power output. Installation must follow quality grouping, directional matching, and sequence requirements to ensure accuracy and performance.
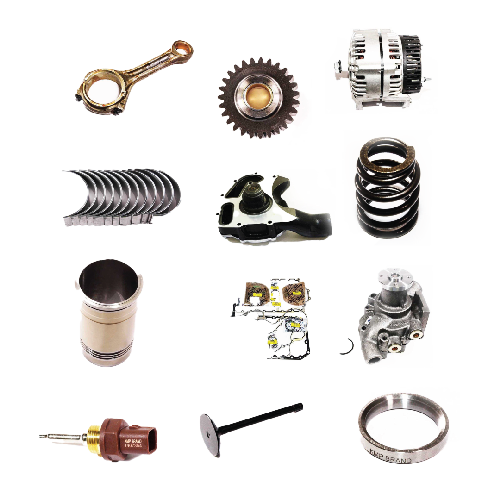
Prior to assembly, pistons and connecting rods should be grouped by weight to ensure balanced engine operation. For a single engine, piston weight differences should not exceed 8 grams, and connecting rod differences should be within 20 grams, preventing vibration and uneven wear.
Each connecting rod's shaft and big-end cap must be matched according to their original markings, with no mismatches or reversed directions. Ensure the side mark on the big-end cap and the arrow on the piston top point toward the fan end of the engine to place the combustion chamber correctly, optimizing combustion efficiency.
To facilitate assembly, heat the piston in boiling water so it slightly expands, allowing easy insertion of the piston pin. The retaining rings at each end of the pin should securely fit into their grooves to prevent pin loosening during operation.
Different diesel engine types, naturally aspirated, turbocharged, and turbo-intercooled, use slightly varied piston ring designs:
Naturally Aspirated and Turbocharged Engines: Both use 5mm thick oil rings. For naturally aspirated engines, the top ring is chrome-plated, while turbocharged engines have molybdenum-coated top rings; the second ring and oil rings are compatible.
Turbo-Intercooled Engines: These engines use uniquely structured rings, with a trapezoidal top ring, twisted second ring, and 4mm oil ring.
Piston Ring Gap Positioning: Ensure rings can rotate freely in the grooves, and set the gap angles as follows:
Top ring's gap at a 30° angle to the piston pin axis
Second and third ring gaps offset by 120°
Cylinder Liner and Piston Ring Matching: When replacing the cylinder liner, use molybdenum-coated rings with chrome-plated liners to avoid excessive friction, which could lead to scuffing.
The oil pump provides lubrication pressure to the diesel generator and must be installed according to the following requirements.
Mounting and Drive: The oil pump is fixed to the engine block with two M10 bolts, driven by gears on the camshaft. Check camshaft rotation after installation; if it's stiff, adjust shim thickness to ensure proper axial clearance.
Inspection and Testing: After installation, perform a test rotation to confirm there's no unusual noise or binding, ensuring the oil pump can deliver stable lubrication during engine operation.
The gear system is essential for diesel engine transmission, requiring precise clearances and alignment.
Gear Housing Positioning and Assembly: Install the idle gear shaft to position gears accurately. After sequentially installing each gear according to markings, check axial and gear clearances.
Clearance Adjustment: If clearances don't meet specifications, adjust by replacing gears or repositioning the gear housing. Loosen housing bolts and lightly tap if necessary to adjust the gear position.
The fuel injector is a key component of the fuel injection system, crucial for fuel delivery accuracy.
Tightening and Height Requirements: For S-type and P-type injector clamps, tighten nuts to a torque of (60±10) N·m. The injector tip should protrude 2.8 to 3.2 mm below the cylinder head surface for precise fuel injection.
Inspection and Testing: Conduct injection testing to check for even spray patterns and absence of leaks, ensuring optimal combustion efficiency during operation.
The crankshaft torsional vibration damper reduces torsional vibrations, ensuring stable engine operation.
Damper Structure and Function: Diesel engines typically use rubber torsional dampers, with a rubber ring between the inner and outer rings to absorb torsional energy and reduce crankshaft vibrations.
Maintenance and Inspection: Regularly check for misalignment or dislocation of inner and outer ring marks, and inspect the rubber ring for extrusion or cracks. Replace the damper if necessary. Additionally, replace the damper if flywheel bolts loosen or break, or if the damper has exceeded 100,000 km to ensure reliability.
Tightening Requirements: Secure the damper nut with a torque of 392 to 441 N·m to prevent loosening during operation.
The reliable operation of a diesel generator relies on precise assembly and adherence to standardized procedures for key components. The piston and connecting rod assembly demands strict quality grouping and directional marking for proper combustion chamber positioning. The oil pump installation requires precise axial clearance to ensure smooth lubrication. Gear system assembly involves careful positioning and gap adjustments for stable transmission. Fuel injector installation must meet specific torque and height requirements to guarantee accurate fuel spray. Lastly, the torsional vibration damper absorbs operational vibrations, with periodic checks extending engine life. These meticulous assembly requirements and adjustments ensure the diesel generator operates efficiently, stably, and durably.