Gas Turbine vs. Internal Combustion Engine for Generator Sets
On this page
In modern distributed power generation systems, gas turbine generator sets and internal combustion engine generator sets play an irreplaceable role as core equipment. Their thermoelectric output characteristics directly affect the system's efficiency, stability, and economic viability. Therefore, understanding the features and applicable scenarios of these two types of generator sets is crucial for optimizing distributed power generation systems. Depending on system scale, environmental conditions, and load variations, gas turbine generator sets and internal combustion engine generator sets each demonstrate unique advantages and applicability.
In distributed power generation systems, power generation efficiency and exhaust gas temperature are two critical indicators for evaluating performance. Internal combustion engine generator sets typically exhibit higher power generation efficiency at the same power output, with common models achieving efficiency rates between 30% and 40%, and some even exceeding 35%. However, the exhaust gas temperature of internal combustion engine generator sets is relatively low, usually around 300°C, which limits the further utilization of waste heat to some extent.
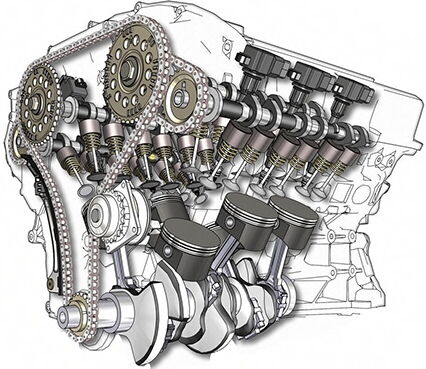
In contrast, gas turbine generator sets have slightly lower power generation efficiency, generally ranging from 30% to 35%, but their exhaust gas temperature is significantly higher, often exceeding 450°C, with some units even surpassing 500°C. This high-temperature exhaust gas can be utilized through waste heat recovery boilers to generate high-pressure steam, which can be further used for heating, cooling, or driving steam turbines for power generation. Through this approach, gas turbine generator sets can form a gas-steam combined cycle system, increasing power generation efficiency to 45% to 50%, with some large units even exceeding 55%. Therefore, gas turbine generator sets demonstrate significant advantages in scenarios requiring efficient waste heat utilization.
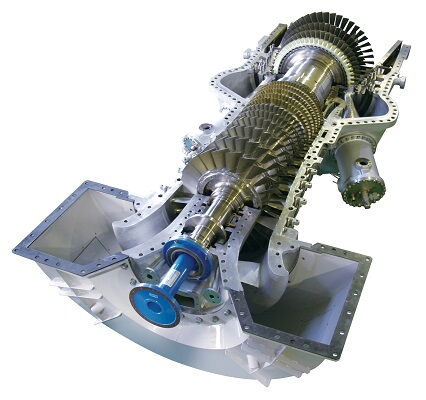
The performance of gas turbine and internal combustion engine generator sets is closely related to environmental conditions. Gas turbine generator sets are more sensitive to changes in altitude and ambient temperature, with output power and efficiency decreasing under high altitude and high-temperature conditions. However, the impact of load variations on both types of generator sets is more pronounced.
In actual operation, distributed power generation systems typically operate under partial load conditions. The thermal efficiency of gas turbine generator sets decreases significantly when the load is reduced, while the thermal efficiency of internal combustion engine generator sets tends to increase with decreasing load. Although the overall thermoelectric efficiency (the sum of thermal efficiency and power generation efficiency) of both generator sets is roughly the same under rated conditions, internal combustion engine generator sets exhibit superior performance under variable load conditions, making them especially suitable for applications with significant load fluctuations.
There are significant differences in waste heat utilization between gas turbine and internal combustion engine generator sets. The waste heat of gas turbine generator sets is primarily concentrated in high-temperature exhaust gases, which can be used to produce high-pressure steam through waste heat boilers, further improving energy utilization efficiency. This method of waste heat utilization makes gas turbine generator sets stand out in industrial sectors, particularly in scenarios requiring combined cycle systems.
The waste heat from internal combustion engine generator sets is divided into two parts: one part comes from cylinder liner cooling water, which is at a lower temperature and mainly used for domestic hot water preparation and heating; the other part comes from exhaust gas waste heat, with a temperature between micro and small gas turbine generator sets, which can be used to drive absorption chillers or produce steam. Due to the lower temperature of the cylinder liner cooling water, the waste heat utilization of internal combustion engine generator sets is more limited, but its waste heat distribution is relatively uniform, making it suitable for thermal energy applications with lower temperature requirements.
There is a significant difference in gas inlet pressure requirements between gas turbine and internal combustion engine generator sets. Small gas turbine generator sets typically require high or medium-high pressure gas inlet pressure, necessitating the inclusion of gas compressors. The gas compression process consumes a large amount of energy, potentially affecting the actual output power of small gas turbine generator sets, with some projects even consuming 15% to 20% of the output power. This high-pressure requirement somewhat limits the application flexibility of gas turbine generator sets, especially in cases where the natural gas inlet pressure is low.
Internal combustion engine generator sets and micro gas turbine generator sets, on the other hand, generally operate under low or medium-pressure conditions, without the need for additional gas compression equipment, thereby reducing system complexity and energy consumption. This gives internal combustion engine generator sets an advantage in applications with lower gas source pressure.
Compared to traditional gasoline and diesel generators, gas generator sets offer significant environmental benefits. They use natural gas, liquefied petroleum gas, or biogas as fuel, greatly reducing environmental pollution. Additionally, gas generator sets have a simple structure, are safe and reliable to use, and provide stable output voltage and frequency, making them suitable for a variety of applications. Their highly integrated design allows for quick installation, making them particularly suitable for temporary or mobile projects.
In terms of adaptability, gas turbine generator sets offer broader fuel adaptability, capable of using high-sulfur, dusty fuels, and even crude oil and high-sulfur residual oil as fuel. Although gas turbine generator sets do not match the power generation efficiency of internal combustion engine generator sets, they excel in waste heat utilization efficiency, especially in combined cycle systems. On the other hand, internal combustion engine generator sets require higher fuel quality, particularly being sensitive to the moisture and hydrogen sulfide in coke oven gas, requiring measures to prevent sulfuric acid corrosion.
In summary, gas turbine and internal combustion engine generator sets each have their strengths and are suitable for different application scenarios in distributed power generation systems. Gas turbine generator sets have significant advantages in high-temperature waste heat utilization and combined cycle systems, making them ideal for large-scale industrial applications requiring efficient energy utilization. Their high reliability and adaptability to low-quality fuels allow gas turbine generator sets to maintain stable output even in complex environments.
Internal combustion engine generator sets, with their higher power generation efficiency and superior performance under variable load conditions, are better suited for smaller-scale systems with fluctuating loads. Their low-pressure gas inlet requirements and lower waste heat temperature make internal combustion engine generator sets particularly effective in applications requiring flexibility and lower costs.
When selecting the appropriate generator set type for specific applications, it is essential to comprehensively consider factors such as system scale, environmental conditions, load variations, fuel type, and other engineering conditions to achieve optimal system performance and efficient resource utilization.