Cylinder Misfire in Diesel Generators: Causes and Solutions
On this page
Cylinder misfire in a diesel generator refers to a situation where one or more cylinders in a multi-cylinder engine fail to operate properly or work intermittently. This issue leads to unstable generator performance, characterized by rough operation, vibrations, irregular sounds, loss of power, and stalling. Additionally, exhaust emissions may include black smoke, and the exhaust pipe may exhibit oil dripping and a fuel odor. To effectively diagnose and repair cylinder misfire in diesel generators, it is crucial to understand its primary causes and appropriate solutions.
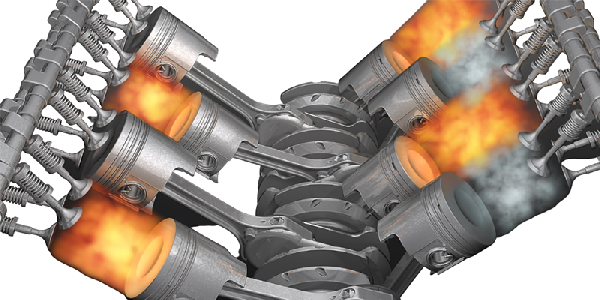
Understanding the main causes of cylinder misfire is essential for effective diagnosis and repair. Here are the primary causes.
Intake and exhaust valves are vital for the proper functioning of a cylinder in a diesel generator. These valves control the entry and exit of gases within the cylinder. If the valves suffer from erosion, detachment, or seal failure, the combustion process inside the cylinder will be severely affected, leading to misfire. Valve erosion is often caused by high temperatures, excessive fuel pressure, or poor fuel quality, which in turn affects cylinder sealing and combustion efficiency.
When a generator operates beyond its design load, it imposes excessive mechanical stress on the cylinders. For instance, piston rings may break under excessive load, preventing the cylinder from maintaining normal pressure levels. Issues such as poor valve sealing or cylinder scuffing may also arise, reducing compression pressure and affecting the generator's overall performance and lifespan.
Modern diesel generators rely on electronic control systems to accurately control injector operation. Any faults in the electronic control system, such as power supply issues or poor wiring connections, can lead to improper injector functioning. If the injector fails to inject fuel at the correct time, the combustion process in the cylinder will be disrupted, affecting the generator's efficiency and stability.
The fuel pump is responsible for delivering fuel into the cylinder under high pressure. Proper functioning of the pump's plunger and outlet valve is crucial for engine performance. Fuel pump failures, such as plunger wear or valve malfunction, can lead to incorrect fuel timing or insufficient fuel delivery, adversely affecting combustion and causing power loss and instability.
The use of low-quality or inappropriate fuel can negatively impact the fuel injection system. Poor-quality fuel may cause clogging or sticking of the injectors, affecting fuel spray and cylinder performance. The quality of the fuel directly impacts the uniformity of fuel injection and combustion completeness, making it essential to use high-quality fuel for proper generator operation.
In winter conditions, the increased viscosity of engine oil can make starting the generator more difficult. During a cold start, individual cylinders may experience unstable idling and fail to operate correctly due to low temperatures. However, as the engine warms up, the oil becomes more fluid, and the cylinders typically return to normal operation. Therefore, appropriate preheating and use of suitable oil are crucial for ensuring smooth winter starts.
Cylinder misfire in a diesel generator typically presents several noticeable symptoms. Understanding these symptoms and conducting effective diagnostics are critical for resolving the issue. Common symptoms and diagnostic methods are as follows.
If you suspect that the valve is not sealing properly, you can test it by adding a small amount of engine oil to the cylinder. After rotating the crankshaft a few turns, remove the injector and move the cylinder piston to the top dead center. Use a low-pressure compressed air nozzle to seal the injector port, and place a listening device near the intake and exhaust ports. If you hear a "hissing" sound, this indicates a valve leak. If you hear a "whooshing" sound, rotate the crankshaft one more turn and check again. This method helps confirm the condition of the valve seals.
If the generator operates normally but emits black smoke or oil drips from the exhaust pipe, and the oil level increases, the injectors may be faulty. Injector issues can lead to uneven fuel spraying, affecting combustion. Checking for clogs or sticking in the injectors and ensuring proper injector function is key to resolving such problems.
A blown cylinder head gasket can cause coolant leakage, affecting engine cooling. Check for bubbles emerging from the radiator cap or unusual sounds from the crankcase, which are common signs of a blown gasket. Replacing the damaged gasket promptly restores normal engine operating temperature and performance.
If the above checks do not resolve the issue, further inspection is needed to determine if the cylinder's compression ratio is insufficient or if there are other mechanical faults such as bent connecting rods. Checking the cylinder's compression ratio helps determine if it can provide adequate compression pressure, while bent rods can lead to abnormal cylinder movement.
Addressing cylinder misfire in diesel generators requires effective remedial actions. Here are the measures for the main causes.
For valve erosion or detachment, repair or replacement is necessary. Check the valve sealing to ensure it effectively controls gas flow into and out of the cylinder, restoring proper cylinder function.
For mechanical faults caused by overloading, inspect components such as piston rings and valve seals. Repair or replace damaged parts to restore normal cylinder compression and sealing, ensuring stable generator operation.
Ensure the electronic control system operates correctly by checking the power supply and connections. Repair or replace faulty components in the system to ensure proper injector operation.
For fuel pump issues, inspect the pump's plunger and outlet valve. Repair or replace faulty components to ensure accurate fuel timing and delivery, improving engine efficiency.
Use fuel that meets standards to avoid issues caused by poor fuel quality, such as injector clogs or sticking. High-quality fuel enhances combustion efficiency and reduces fault occurrences.
In cold weather, choose appropriate engine oil and preheat the engine to ensure smooth starting and normal operation. Regularly inspect and maintain the generator to adapt to seasonal changes affecting engine performance.
Cylinder misfire in diesel generators not only causes operational instability but may also damage other components. Accurate diagnosis and appropriate repair measures can effectively reduce long-term damage, improve efficiency, and extend the generator's service life. Regular inspection and maintenance, especially during load and seasonal changes, help ensure reliable operation and longevity of the generator.